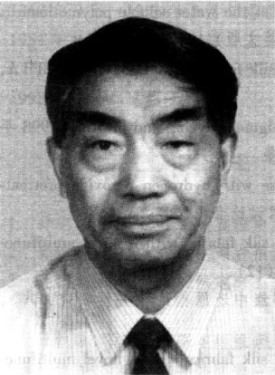
"In 1954, I transferred to the Design Department of the Ministry of Textile Industry, where I was the head of the printing and dyeing design group and the team leader of the Soviet Union's expert study group. I chaired and participated in the Northwest China's First India, Shijiazhuang Printing and Dyeing Factory, Zhengzhou Printing and Dyeing Factory, Beijing Printing and Dyeing Factory, etc. A number of large-scale printing and dyeing plant design work." Xu barn said that at that time it was the large-scale construction period of China's textile industry. "In 1973, I went to the Qingjiang Printing and Dyeing Factory of Huaiyin City to serve as the deputy director of the Planning and Construction Department. At that time, I was young and I stayed up all day and night. I completed the design task book in just one week. The factory building is in a zigzag shape, with a roof and insulation layer, and the equipment is smooth. The jagged arrangement, the uniform lighting of the workshop, the exhaust ventilation, and the non-driping of the winter workshop, which were more advanced at the time, completed the construction, installation and trial production of the first phase in less than a year. In 1977, the Production Department of the Ministry of Textiles organized the whole country. 66 printing and dyeing companies held a live meeting in Huaiyin City to promote the experience of Qingjiang Printing and Dyeing Factory. According to Xu Barn's memories, later, Jiangsu Yancheng Printing and Dyeing Factory, Yangzhou Printing and Dyeing Factory, Nantong Bayi Printing and Dyeing Factory, Shandong Zaozhuang Printing and Dyeing Factory, Jilin Siping Printing and Dyeing Factory, etc. When the new factory was under construction, related personnel came to visit the Qingjiang Printing and Dyeing Factory.
In 1985, Kunshan Printing and Dyeing Plant expanded its new workshop. Xu Barn proposed to change the plant to east-west direction and serrate southwards, in order to facilitate the lighting of the workshop and avoid the winter fog discharge, but the implementation of the program must move 10,000 volts high-voltage lines. He took the plan and based his arguments on trying to persuade the county leader to move the high-voltage line to ensure the rational construction of the new factory. In June 1986, he was transferred to Kunshan Printing and Dyeing Factory as chief engineer and successfully completed the construction, installation and commissioning of the new plant, making this plant one of the “Top Ten Dyeing and Finishing Enterprises†in the country.
Innovation In the 1960s, Xu Barn assisted the Changzhou Yifengchang Dyeing Factory in summarizing the technical experience in producing heavy khaki fabrics during the printing and dyeing section of the Jiangsu Textile Department, and found out that the mercerized fabrics were “rich, full, clean, tight, and wideâ€. “Songâ€'s six-character experience; helped Changzhou Jiufeng Printing and Dyeing Factory to revise the dyeing and finishing process of corduroy fabrics, summed up the technical experience in producing corduroy fabrics, and laid a solid foundation for Changzhou’s khaki fabrics and corduroy fabrics. basis.
With regard to the phenomenon that the ratio of energy consumption to total cost of enterprises continues to increase, Xu barn went deep into the workshops and teams to investigate and work with operators to explore new ways to save energy. Through various tests, he used the heat balance measurement algorithm to formulate the energy consumption quota, which enabled the energy consumption of the Qingjiang Printing and Dyeing Plant to be effectively controlled. Xu Barn has adopted new energy-saving technologies and new technologies in the transformation of traditional energy-saving technologies. It has promoted the use of cold-rolled heap short-flow alkali-oxygen-bath technology, loose-pile mercerizing technology, short-flow wet steam dyeing of reactive dyes, and cold-rolled reactors. Dyeing process, organic heating body heating furnace, and energy-saving singeing and other energy-saving technologies and equipment have achieved remarkable results.
In the late 1980s, Xu Barn studied the short-flow pretreatment process for dyeing and finishing that prevailed in Western Europe, and processed the alkali-oxygen-bath process at the Kunshan Printing and Dyeing Plant in a short process to perform traditional three-step desizing, scouring, and bleaching processes. The reforms have achieved results on the thick khaki fabrics and passed the appraisal of the former Ministry of Textile Industry to promote them in Suzhou. In addition, when processing pure cotton plain weave fabrics, Xu Barn summarized the one-step cold-rolling one-step method per 10,000 meters. Compared with the traditional three-step process, although the consumption of chemicals is 68.39 yuan, the cost of water, electricity and gas Saved 678.8 yuan.
In May 1990, Xu Barn retired as the chief editor of the "Dyeing and Finishing Technology" magazine and was a technical consultant for a number of printing and dyeing companies. He continued to serve first-line production.
In 1991, at the 2nd National Symposium on Dyeing and Finishing, Xu Barn introduced the use of alkali-oxygen, one-bath and short-flow process technology for khaki thick fabrics and cold-rolling, alkali-oxygen, one-bath process for pure cotton fabrics and their savings. With experience in energy and cost reduction, new processes have been adopted by companies. However, in a wide range of applications, it is also exposed that the cold-rolling reactor technology can not meet the quality requirements for certain thick and dense fabrics, especially the key quality indicators of cotton fabrics.
In response to the problems in popularization and application, Xu Barn organized dyeing and finishing technics, equipment, auxiliaries, and other experts and Kim Hyong-soo, Cai Mingxun, Shen Yuqing and other professors to further explore and practice, through the amendment cold-reactor process, using core cold-rolled process fluid, The process was divided into three stages: center-driven rolling stacking, high-temperature hot alkali treatment, and high-efficiency water washing, and finally succeeded. In 1994, at the Third National Symposium on Pretreatment of Dyeing and Finishing, Xu Barn introduced the practical experience of using high-temperature hot alkali treatment after cold reactors, so that the cold-rolled reactor alkali oxygen one-bath pretreatment short-flow process was promoted throughout the country. .
Xu Barn has long been engaged in the design and construction of dyeing and finishing plants, actively promoted new dyeing and finishing processes, new technologies, promoted short-flow pre-treatment, and promoted energy conservation and consumption reduction. At the same time, he also eagerly organized academic activities. He never failed to write. He has published more than 50 papers for dyeing and finishing, and he has written 4 books, such as "Pretreatment for dyeing and finishing fabrics" and "Energy saving for dyeing and finishing."
In March this year, the Dyeing and Finishing Professional Committee of the Chinese Textile Engineering Society awarded Xu Barn with the “Lifetime Honor Awardâ€. Xu Barn said: "I will strive for our country's dyeing and finishing career for life."
This is a product designed for paper-cut or embroidery products and their derivatives. They are handmade and made with Chinese characteristics and traditional methods.
Embroidery: The hand-embroidered bag material is made of high-quality fabrics, hand-embroidered by a line of embroidered women, and carefully needle-stitched. The Embroidered Brooch is designed with traditional Chinese butterfly shapes and flower shapes as a sample, traditional and retro.
Paper-cut: Taken from Chinese traditional red paper, the paper is cut by Chinese non-genetic inheritors and senior art masters. The shape depends on the local scenery or legends, especially the portrait paper-cut, which is vivid and vivid.
Paper-Cut Painting,Glass Sticker,Papercut Printing,Paper-Cut Painting Glass Stickers
Ningxia Yimeng Liyi Culture and Art Co., Ltd. , https://www.fuzhaoe.com